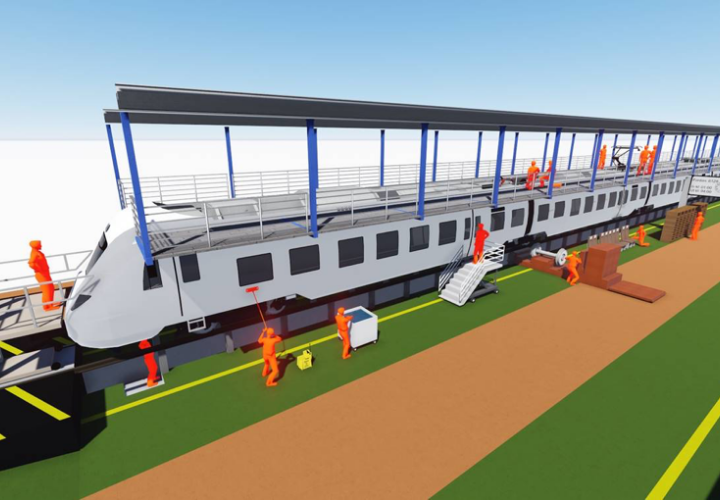
Workshop design
The diagram shows a workplace for carrying out maintenance on a multiple-unit train where different jobs can be carried out in parallel so as to fit in with roster downtime planning. Concurrent flows enable engineers to work on the rolling stock’s roofs, car bodies, frontal structures, interiors, and underframes independently of each other.
Normally, the train is stationary at the workplace, which is equipped for different work tasks. Hence, there are no lifting jacks in the diagram; instead, mobile wheel set drop tables dock to outlets in pillar-supported pits to allow access when changing wheelsets, for example. Roof-mounted equipment is replaced using a telpher track that runs along the whole track at each workplace. The entire roof system in the workshop is suspended from steel structures, which means there are no support pillars descending to the production areas. Consequently, there are no obstacles to the changing of modules in underframes, which requires space for forklift operations, for example.
The workshop dimensions also facilitate efficient maintenance setup. The area between the tracks in the workshop is well suited for the transport of materials, with unobstructed space between the rolling stock’s carriage bodies in the production hall. This creates an independence between the tracks, whereby the different work tasks do not interfere with each other in the facility. Similarly, there are at least ten metres from the gate to the front of the rolling stock, allowing for efficient warehouse logistics in the transport corridors and well-organised work on the frontal structures of the rolling stocks.
Terminal services are co-ordinated with maintenance, i.e., the rolling stock is cleaned, supplies are topped up, water is pressurised, and sewage tanks are emptied. This means that the train is ready to operate when it leaves the workshop and does not have to be moved to another facility section to be readied for service.